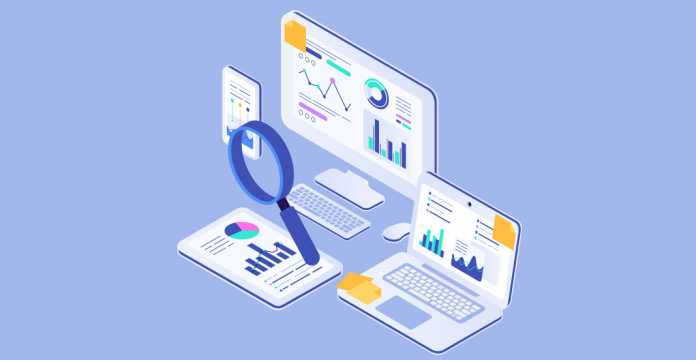
In today’s competitive business environment, it is imperative that enterprises ensure their products/services are of the highest quality. Also, customer satisfaction is a critical metric to retain and grow customer relationships. In this article, we will explore what root cause analysis is, how to plan for it, and different techniques and methods involved with the help of an example.
What is Root Cause Analysis (RCA)?
Root Cause Analysis ( RCA) is a systematic concept that involves a set of problem-solving approaches used to determine the underlying cause of an issue of non-compliance or consistency. Examination of the root cause is the method of recognizing, explaining, and solving a problem. The root cause of a non-conformance, flaw, or malfunction has often been defined as an underlying or fundamental explanation. Also, the word “root cause” can often be applied to as the particular point in the causal chain where the implementation of disciplinary action or intervention will avoid non-conformance.
Using root cause analysis to evaluate concerns or incidents should help you achieve the primary objective of:
- What did happen?
- How it did happen?
- Why does it go bad?
- Activities for stopping the recurrence of the problems
In the end, the study of the root cause comes down to three priorities. The first goal is to find the root cause of a problem or occurrence, just as the name implies. The second aim is to consider how to cure, reward, or benefit from root cause problems. The third and most significant purpose is to apply what you understand from the study to eliminate potential problems.
Why Perform Root Cause Analysis?
Repetitive issues in the processing are a cause of pollution. Waste in the form of downtime on computers, product rework, increased scrap, and time and money spent “fixing” the problem. Many times we may assume the problem is fixed, but in fact, we only addressed the symptom which was the first level of the problem and not the root cause itself. RCA methods and tools are not limited to manufacturing process problems only. Many industries are applying RCA techniques in various situations and are using this structured approach to problem-solving. Some examples of where RCA is being used include, but are not limited to: A Root Cause Analysis, done correctly, will recognize breakdowns in the procedures or structures that have led to the non-conformance and decide how to keep it from occurring again. An RCA is conducted to assess what happened, why it happened, and then determine what needs to be strengthened or modified. Repeat issues may be solved by careful use of the RCA.
Processes in the Workplace
- Problems of quality management
- Analyzing risk accidents
- Security-related circumstances or an overview of injuries
- Analyzing deficiencies in infrastructure and maintenance
- Shift management practices or quality development
- Computer or Software Analysis
How Do You Plan for a Root Cause Analysis?
It’s necessary to spend time planning for a root cause review by conducting the initial research, finding the required workers, and forecasting concerns that may occur during the RCA conference. A typical example of a puzzle maker planning for an RCA is. Even the most skilled puzzle maker, who could know tips and tricks for significant puzzle building, can not be useful if a piece of the puzzle is missing or there is no space for puzzle creation.
Similarly, if crucial information is lacking, staff members are unavailable, or the buildings are inefficient, staff can’t complete a root cause study. So make sure you gather documentation, identify key team members, and plan for the unexpected before you meet with the RCA.
Change Analysis/Event Analysis
Another valuable way of evaluating root cause behavior is to analyze the developments leading up to a case closely.
This approach is beneficial because there is a wide range of plausible triggers. Rather than looking at the exact day or hour when something went wrong, we’re looking for a more extended period and having a broader perspective.
1. Next, we will mention any possible trigger that contributes to a case. It can be for better or worse or positive any time a transition has happened.
Example: Let’s presume the case we’re going to be studying is an uncharacteristically good New York City shopping day, and we wanted to know why it was so amazing so we could try and reproduce it. First, for each of the main clients, each case, and every potentially related shift, we will list every contact point.
2. Second, we will categorize any transition or occurrence by how much impact we exercised on it. We may identify as Internal / External, Owned / Unknown, or anything similar.
Example: In our fantastic sales day scenario, we’d start working out stuff like “Sales representative launched new slide deck on social effects” (Internal) and other activities like “Last day of the quarter” (External) or “First day of spring” (External).
3. Thirdly, we will go case by case to determine whether or not the occurrence was an unrelated factor, a combined factor, a contributing factor, or a possible root cause. This is where the majority of the research exists, and it is here where such methods such as the 5 WHYs of root cause analysis can be practiced.
Example: In evaluation, we discover that an unexpected aspect was our fancy new Advertising Slide Deck. Still, a contributing factor was the fact that it was quarter-end. One part, though, was established as the possible root cause: the area’s Sales Lead moved to a new apartment with a shorter commute, ensuring she began to meet with customers 10 minutes earlier in the last week of the quarter.
4. Fourthly, we are trying to see if the root cause can be repeated or remedied.
Example: While not everybody may relocate to a new location, the company determines that if Sales Reps turn up an additional 10 minutes early to consumer meetings in a quarter’s final week, they will be able to duplicate the root cause performance.
To learn more about identifying root causes that are causing issues and to find optimal solutions to your problems, consider pursuing quality management certification courses from Invensis Learning today!
Some of the popular quality management certification courses that individuals and enterprise teams can take up are:
I’m not that much of a internet reader to be honest but your sites really nice, keep it up! I’ll go ahead and bookmark your site to come back down the road. All the best